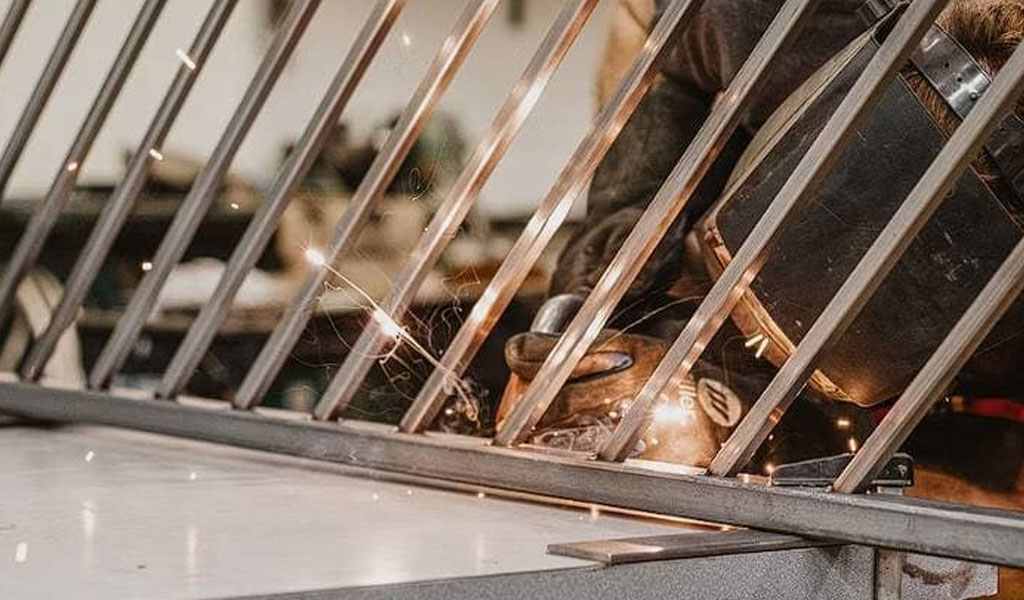
Se cree comúnmente que la soldadura MIG de aluminio es difícil. Sin embargo, esto no es cierto y depende en gran medida del estado del aluminio y de la configuración de la soldadura. Se obtienen resultados mediocres si no se dedica el tiempo y el esfuerzo necesarios para prepararse adecuadamente.
Si comparamos la soldadura MIG con la soldadura TIG de aluminio, la primera es más sencilla y requiere menos tiempo. Sin embargo, si se siguen los pasos y se realizan los preparativos adecuados, la calidad de la unión soldada resultante es idéntica.
Con ese fin, este blog le enseñará cómo preparar adecuadamente este metal común, por qué el aluminio es difícil de soldar, qué gas protector utilizar, cómo configurar correctamente su soldadora MIG y la técnica de soldadura adecuada.
¿POR QUÉ ES TAN DIFÍCIL SOLDAR ALUMINIO CON MIG?
El aluminio requiere procedimientos de soldadura MIG muy diferentes a los del acero. Debido a sus propiedades químicas y físicas diferentes, la masa fundida de aluminio es especialmente vulnerable a los defectos de soldadura que pueden debilitar la soldadura. Se puede evitar y lograr una soldadura resistente y duradera con el equipo y los conocimientos técnicos adecuados. Estas características consisten en:
ESPESOR DEL METAL
En comparación con otras piezas fundidas, como el acero al carbono, las piezas de aluminio suelen ser más delgadas. La perforación por quemadura es un problema común al soldar este metal con MIG. Este es un problema común al soldar aluminio y puede acumularse rápidamente si se debe tener cuidado.
SENSIBLE A LAS IMPUREZAS EN UN NIVEL ALTO
El agua, la suciedad y otros contaminantes pueden introducirse fácilmente en las soldaduras de aluminio. Por lo tanto, se deben tomar precauciones adicionales al soldar aluminio con MIG para que el metal no se contamine y debilite la soldadura. Para evitar la contaminación, utilice los gases de protección y los materiales de relleno adecuados.
PUNTO DE FUSIÓN BAJO
El punto de fusión del aluminio es de alrededor de 1220 grados Fahrenheit. El aluminio oxidado se funde a tan solo 3700 grados Fahrenheit. El bajo punto de fusión del aluminio hace que sea complicado trabajar con él en comparación con el acero, cuyo punto de fusión se encuentra entre 2600 y 2800 grados Fahrenheit.
Como soldar aluminio requiere eliminar el óxido que actúa como escudo, es necesario limpiar previamente las piezas a fondo.
ALTA POROSIDAD
El aluminio absorbe hidrógeno cuando se calienta hasta alcanzar el estado líquido, lo que lo hace extremadamente vulnerable a la contaminación. Cuando el hidrógeno forma parte de una masa fundida, tiende a cristalizarse al enfriarse. Como resultado, el aluminio se vuelve poroso debido a la formación de burbujas. La soldadura creada con otras aleaciones metálicas no es lo suficientemente resistente como para durar.
CÓMO CONFIGURAR CORRECTAMENTE SU SOLDADORA MIG PARA ALUMINIO
El voltaje correcto para la transferencia de pulverización es sólo una de las muchas variables que deben ajustarse para lograr una soldadura MIG exitosa de aluminio.
Para ayudarlo a evitar problemas comunes, repasemos cada configuración de su soldadora MIG y hablemos sobre el caudal de gas protector.
AJUSTES DE ALIMENTACIÓN DE ALAMBRE
La soldadura MIG de aluminio requiere velocidades de alimentación de alambre mucho mayores que la del acero dulce. Puede encontrar los ajustes MIG en el manual de su máquina de soldar.
Si su máquina no tiene un cuadro en el compartimento de almacenamiento, debe consultar el manual del usuario. También puede verificar los procedimientos de soldadura de aluminio que su empresa ha aprobado.
Sin embargo, si su soldadora MIG no tiene una tabla de configuraciones, puede usar una velocidad de alimentación de alambre 30-100% más rápida que la utilizada para acero dulce, como regla general.
SELECCIÓN DEL AMPERAJE DE SALIDA
Al soldar con MIG, la cantidad de amperaje producido depende de la velocidad con la que se introduce el alambre en la máquina. La soldadura de metal requiere más amperaje y una penetración más profunda cuanto más rápido se mueve el metal.
El amperaje de salida de la soldadora variará según el modelo para una velocidad de alimentación de alambre específica. Es por eso que una máquina puede producir 200 A a una velocidad de alimentación de alambre de 400 IPM y otra puede producir 180 A a la misma velocidad.
El amperaje de salida también se ve afectado por el diámetro del cable. El grosor del cable se relaciona directamente con la corriente que puede transportar. Por lo tanto, la velocidad de alimentación del cable debe ser mayor para que un cable más grueso produzca el mismo amperaje que un cable más delgado.
ACCESORIO DE PISTOLA DE EMPUJE Y TRACCIÓN O CARRETE
Consulta el sitio web del fabricante para ver si tu soldadora es compatible con una pistola de carrete o de empuje y tracción. Si ya tienes una soldadora MIG y una pistola de soldadura de aluminio, puedes conectar todo de acuerdo con las instrucciones del fabricante.
Aunque no siempre es así, ahora se utilizan comúnmente pistolas de carrete o de empuje y tracción en lugar de la pistola MIG estándar. Además, el cable de alimentación de la pistola de carrete debe estar conectado al panel frontal de la máquina de soldar.
Sin embargo, no existen pautas absolutas, ya que algunos fabricantes alimentan la pistola de carrete con el cable de soldadura que también suministra el gas protector.
CAUDAL DEL GAS DE PROTECCIÓN
Para la soldadura MIG de aluminio se requiere un alto caudal de gas protector debido al rápido movimiento de la antorcha requerido.
La soldadura MIG de aluminio requiere un mínimo de 20 pies cúbicos por hora («CFH») cuando se utiliza argón puro, mientras que 15 CFH son suficientes para soldar acero al carbono. Sin embargo, si sus soldaduras son porosas, intente aumentar el flujo a alrededor de 30 pies cúbicos por hora.
Sin embargo, una mezcla de argón y helio requiere un caudal de gas de protección aún mayor. Debido a la baja densidad del helio en comparación con el aire y el argón, puede ser necesario un caudal de hasta 50 CFH. Sin embargo, una mezcla de argón y helio requiere un caudal de gas de protección aún mayor. Debido a la baja densidad del helio en comparación con el aire y el argón, puede ser necesario un caudal de hasta 50 CFH.
PROCEDIMIENTO DE SOLDADURA MIG DE ALUMINIO
Limpieza de superficies de aluminio
La limpieza de la superficie del metal es el primer paso en la soldadura MIG de aluminio. Este procedimiento es esencial porque permite reducir drásticamente los contaminantes ambientales como el polvo y la humedad. La soldadura se vería comprometida sin la eliminación de estos contaminantes. Los disolventes son el medio más eficaz para limpiar el aluminio.
Un ejemplo es la acetona, un disolvente ideal para eliminar el vapor de humedad y limpiar la grasa y los aceites de la superficie de aluminio. Aplique acetona a una toalla de taller o un paño húmedo para limpiar el aluminio y restriegue la superficie.
Oil Eater y otros desengrasantes son dos ejemplos de jabones potentes que funcionan bien para este propósito. Puedes comenzar a soldar cuando termines el procedimiento y las piezas de aluminio estén limpias y secas.
Eliminar la capa oxidada
El punto de fusión del aluminio oxidado es mayor que el del aluminio puro. Se necesitan 3700 grados Fahrenheit para que la capa oxidada se derrita. Para preparar el aluminio para la soldadura MIG, primero retire la capa protectora. Los óxidos de la superficie del aluminio se eliminan fácilmente con un cepillo de alambre de acero inoxidable.
Sin embargo, se debe utilizar un desengrasante para eliminar las impurezas antes de eliminar la capa oxidada. Si no se hace esto, se corre el riesgo de introducir hidrocarburos y otras impurezas en el metal. Tampoco se recomienda que los soldadores principiantes eliminen la capa oxidada con un cepillo de alambre.
Las técnicas alternativas para limpiar el aluminio de óxidos incluyen el uso de soluciones desoxidantes. El aluminio puede resultar dañado si se utilizan demasiadas soluciones químicas, por lo que se debe tener cuidado.
Seleccione el mejor material de relleno para soldadura MIG
Se venden en el mercado varios tipos distintos de electrodos de alambre para soldadura. Es importante considerar cuidadosamente sus requisitos y preferencias de soldadura antes de decidirse por una variedad específica. Existe un tipo especial de electrodos de alambre fabricados para la soldadura MIG de aluminio. La soldadura de metales de aluminio puede provocar defectos como porosidad, pero este diseño exclusivo elimina la necesidad de preocuparse por que eso suceda.
Los metales de aporte ER4043, ER5183, ER4047 y ER5356 tienen un rendimiento excepcional en la soldadura MIG de aluminio. Los electrodos más populares y más vendidos son el ER4043 y el ER5356.
Sin embargo, el ER4043 es mucho más blando que los electrodos ER5356, por lo que es el material de elección para la reparación de carrocerías de automóviles. Al decidir qué material de relleno utilizar, debe tener en cuenta el material de base que va a soldar.
Elija el gas protector
Al soldar aluminio con MIG, es fundamental elegir el gas de protección adecuado para proteger la soldadura. Estos gases evitan que la soldadura se contamine con hidrógeno, oxígeno y nitrógeno presentes en la atmósfera. La alta porosidad, provocada por las burbujas de gas en la soldadura, es el resultado de utilizar el gas de protección incorrecto.
Aunque los alambres MIG con núcleo fundente y otros electrodos MIG especiales se pueden utilizar sin gas protector, en la mayoría de los casos, el gas es necesario para evitar que se formen impurezas en la superficie del aluminio durante la soldadura.
El argón y las mezclas de argón y helio son los gases de protección más comunes para la soldadura de aluminio con gas inerte (MIG). Combine helio y argón para utilizarlos en las secciones más gruesas del aluminio. Sin embargo, los gases de oxígeno y dióxido de carbono no son sustitutos adecuados, ya que oxidarán la soldadura fundida y provocarán daños.
Precalentar el metal
El aluminio se puede precalentar antes de soldarlo para eliminar la distorsión en la unión. Aunque este paso no es estrictamente obligatorio, ayuda a prevenir grietas en las soldaduras de aluminio. Sin embargo, lo mejor sería mantener el calor por debajo de 230 grados Fahrenheit.
Las soldaduras de riel colocadas antes y después de la zona de soldadura ayudan a acelerar el procedimiento de precalentamiento. Cuando se trabaja con láminas de aluminio más gruesas, el precalentamiento es esencial. Los soldadores comunes probablemente necesitarán más calor para soldar láminas de aluminio gruesas con éxito. Por este motivo, se pueden utilizar calentadores de inducción para el precalentamiento.
A la hora de precalentar láminas de aluminio, los sistemas de calentamiento por inducción se encuentran entre las máquinas más seguras y fiables que existen. Estos calentadores tienen un diseño basado en bobinas y ofrecen una mejor regulación de la temperatura que los sopletes, ya que no dependen de una llama abierta.
CONSEJOS Y TRUCOS DE SOLDADURA MIG DE ALUMINIO
A continuación se proporcionan algunos consejos útiles para la soldadura MIG de aluminio.
UTILICE EL MATERIAL DE RELLENO ADECUADO.
Varios materiales de relleno se destacan por su rendimiento superior durante la soldadura MIG de aluminio. La soldadura fuerte de cobre, las láminas de níquel-plata, el alambre de bronce y las láminas de latón son excelentes opciones. Estos componentes se destacan cuando se utilizan junto con electrodos de alambre consumibles, especialmente al formar uniones en T sin barras de respaldo.
Su durabilidad superior a la del acero dulce los convierte en una excelente opción para proteger contra defectos como el agrietamiento. Estos materiales de relleno tienen las cualidades necesarias para superar las dificultades de la soldadura de aluminio, lo que permite a los soldadores producir soldaduras impecables. Sus cualidades resistentes aumentan la confiabilidad y la longevidad general de las uniones soldadas.
LA LIMPIEZA ES ESENCIAL.
Al soldar aluminio, se debe tener en cuenta la propensión natural del metal a la oxidación. Antes de soldar, es esencial limpiar a fondo la superficie para obtener los mejores resultados. Un cepillo de alambre de acero inoxidable es un método eficaz para limpiar la superficie del aluminio y eliminar la capa de óxido.
Los soldadores pueden mejorar en gran medida la calidad de sus soldaduras y reducir la porosidad si toman este cuidado en la preparación del metal. Una limpieza cuidadosa antes de soldar no solo mejora la fusión del metal base con el material de aporte, sino que también da como resultado soldaduras de aluminio más duraderas.
UTILICE MÉTODOS DE DISEÑO DE JUNTAS ADECUADOS.
Los métodos de diseño de las uniones deben seleccionarse cuidadosamente cuando se unen metales de distintas calidades. Esta elección reduce la probabilidad de oxidación y corrosión, lo que da como resultado una conexión segura y duradera entre las distintas partes metálicas. Mantener la integridad de los metales unidos y evitar problemas futuros depende en gran medida del diseño de la unión, que debe considerarse cuidadosamente.
UTILICE UN CEPILLO HECHO DE ALAMBRE DE ALUMINIO.
La mejor opción es utilizar cepillos de alambre de aluminio para eliminar el óxido o la corrosión de las superficies metálicas antes de soldar. Es especialmente importante hacerlo cuando se trabaja con materiales de relleno ricos en hierro.
Los cepillos de alambre de aluminio permiten a los soldadores eliminar a fondo cualquier capa de óxido o de óxido, dejando una superficie lisa e impecable. Esta preparación cuidadosa es crucial para producir soldaduras de alta calidad porque mejora la capacidad del metal base de adherirse y fusionarse con el material de relleno. Al deshacerse del óxido, los soldadores pueden hacer uniones que duren más y tengan menos probabilidades de fallar debido a debilidades estructurales.
AUMENTE EL VOLTAJE PARA LOGRAR UNA MAYOR PENETRACIÓN.
El uso de voltajes más altos durante la soldadura permite una penetración más profunda del material, lo que a su vez reduce la probabilidad de porosidad. La penetración puede ser hasta un 50 % más profunda que con los métodos estándar. Sin embargo, se debe tener cuidado y ajustar el voltaje de manera adecuada para evitar que se quemen involuntariamente las láminas de metal.
Los soldadores pueden encontrar el punto óptimo entre la penetración y la protección de la pieza de trabajo mediante el ajuste de la tensión. Este ajuste fino protege la soldadura y garantiza la durabilidad y la estabilidad estructural de las láminas metálicas unidas.
SOLDADURA EN RÁFAGAS CORTAS
El aluminio puede calentarse demasiado fácilmente durante la soldadura, por lo que es mejor utilizar pasadas cortas e intermitentes en lugar de una sola pasada larga. Al permitir que el metal descanse y se enfríe entre las soldaduras, esta técnica reduce la probabilidad de que el metal se sobrecaliente y se deforme.
Este método evita la acumulación de calor excesivo que, de otro modo, podría debilitar la soldadura y el componente de aluminio. Para evitar los problemas que surgen del sobrecalentamiento del aluminio, los soldadores pueden mejorar el control del proceso de soldadura limitando la cantidad de calor aplicada y proporcionando breves intervalos de enfriamiento.
DESPUÉS DE SOLDAR, RETIRE EL CABLE.
El cable de alimentación debe desconectarse rápidamente en su base al soltar el gatillo de la pistola. Dejar el cable en la pistola después de soldar no es una buena idea. La calidad de la soldadura disminuye a medida que el cable se enfría porque se acumula dentro del charco de soldadura.
Al retirar rápidamente el alambre de la pistola, los soldadores evitan que se enfríe en su interior, lo que a su vez reduce las salpicaduras. Este paso preventivo mejora la calidad y el aspecto de la soldadura terminada al reducir la cantidad de salpicaduras que se producen durante el proceso de soldadura. La mejora de la calidad de la soldadura y la reducción del tiempo de limpieza después de la soldadura son dos beneficios de este esfuerzo adicional.
CONCLUSIÓN
La soldadura MIG de aluminio suele considerarse difícil debido a sus propiedades químicas y físicas únicas. El punto de fusión del aluminio es de alrededor de 1220 grados Fahrenheit, lo que lo hace más susceptible a defectos de soldadura. Para evitar la contaminación y debilitar la soldadura, es esencial utilizar los gases de protección y los materiales de relleno adecuados.
El bajo punto de fusión del aluminio hace que sea más difícil trabajar con él en comparación con el acero, cuyo punto de fusión se encuentra entre 2600 y 2800 grados Fahrenheit. Para garantizar una soldadura resistente y duradera, es fundamental disponer del equipo y los conocimientos técnicos adecuados. El voltaje correcto para la transferencia de pulverización y el caudal de gas protector son esenciales para una soldadura MIG exitosa del aluminio.
Los ajustes de alimentación de alambre para la soldadura MIG de aluminio requieren velocidades más altas que las de acero dulce. El amperaje de salida depende de la velocidad del alambre que se alimenta a través de la máquina y del diámetro del alambre. El carrete o el accesorio de pistola de empuje y tracción también son cruciales, y el cable de alimentación debe estar conectado al panel frontal de la máquina de soldar.
Para la soldadura MIG de aluminio se requiere un caudal elevado de gas de protección debido al rápido movimiento del soplete. Se requiere un mínimo de 20 pies cúbicos por hora (CFH) para argón puro, mientras que 15 CFH son suficientes para soldar acero al carbono. Sin embargo, una mezcla de argón y helio requiere un caudal aún mayor.
El primer paso para soldar aluminio con MIG es limpiar la superficie del aluminio, lo que elimina los contaminantes ambientales como el polvo y la humedad. Los disolventes como la acetona y los devoradores de aceite son eficaces para limpiar el aluminio. El punto de fusión del aluminio oxidado es mayor que el del aluminio puro, y la capa oxidada necesita 3700 grados Fahrenheit para fundirse. Es esencial fregar la capa oxidada, pero se recomienda utilizar un desengrasante o soluciones para eliminar el óxido.
La elección del mejor material de relleno para soldadura MIG depende de los requisitos y preferencias de soldadura. Se fabrica un tipo especial de electrodo de alambre para la soldadura MIG de aluminio, lo que elimina la necesidad de defectos como la porosidad. La soldadura MIG de aluminio es un proceso muy eficaz, y los metales de relleno más populares son ER4043, ER5183, ER4047 y ER5356. El material base utilizado para la reparación de carrocerías de automóviles es más blando que los electrodos ER5356, lo que lo convierte en el material preferido para la soldadura. El gas de protección es esencial para proteger la soldadura del hidrógeno, el oxígeno y el nitrógeno de la atmósfera. Los gases de protección habituales incluyen argón y mezclas de argón y helio.
Precalentar el metal es fundamental para evitar grietas en las soldaduras de aluminio, pero lo mejor es mantener la temperatura por debajo de los 230 grados Fahrenheit. Se pueden utilizar calentadores de inducción para precalentar, pero no es estrictamente necesario.
Para garantizar los mejores resultados, utilice el material de relleno adecuado, limpie bien la superficie y utilice métodos de diseño de juntas adecuados. Utilice cepillos de alambre de aluminio para eliminar el óxido o la corrosión de las superficies metálicas antes de soldar, lo que dará como resultado juntas más duraderas. Aumente el voltaje durante la soldadura para lograr una mayor penetración, lo que reduce la probabilidad de porosidad.
Suelde en ráfagas cortas para evitar el sobrecalentamiento y la deformación. Esta técnica permite que el metal descanse y se enfríe entre soldaduras, lo que reduce la probabilidad de sobrecalentamiento y la acumulación de calor excesivo. Después de soldar, desconecte el cable de alimentación en su base y retírelo para evitar salpicaduras y mejorar la calidad de la soldadura.
Enlace:¿CÓMO SOLDAR ALUMINIO CON MIG?
Etiquetas importantes: Torneado CNC, Prototipado Rapido, Fabricación de moldes