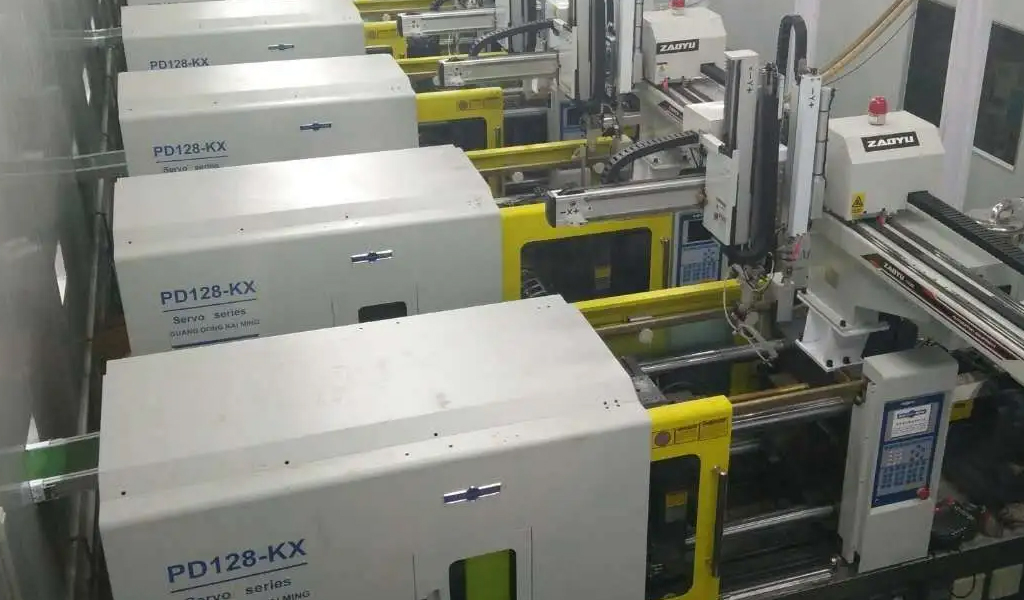
Las recientes innovaciones en la construcción de herramientas con canales conformados de calentamiento y enfriamiento abren nuevas e interesantes posibilidades para diseños de piezas con un rendimiento mejorado y costos más bajos. Los desarrolladores e ingenieros de productos ahora tienen acceso a nuevas técnicas posibles gracias a la fabricación aditiva que prometen enormes beneficios en productividad, ahorro de costos y calidad de las piezas terminadas. Echemos un vistazo a algunos de los desafíos que imponen las herramientas de moldeo por inyección tradicionales y cómo se superan con estos métodos.
¿Qué sucede dentro de la herramienta durante la inyección?
Primero lo básico. Un gran trozo de herramientas de molde de acero o aluminio está esencialmente «frío» en relación con el calor del plástico fundido que se inyecta en él. A medida que el plástico fluye hacia el molde y llena la cavidad, la herramienta absorberá calor residual y eventualmente se alcanzará un cierto equilibrio térmico. Sin embargo, si la diferencia de temperatura inicial es demasiado grande, existe el peligro de que el plástico se deforme.
Una vez que la pieza se ha inyectado completamente, la herramienta ahora caliente debe enfriarse nuevamente para permitir que la pieza de plástico fundida se solidifique y preparar el molde para la siguiente inyección o «disparo».
Por lo tanto, las herramientas de molde tradicionales se fabrican con canales de enfriamiento y, antes de la llegada de la impresión de metal 3D, estos canales estaban necesariamente en línea recta porque simplemente se perforaban en el molde. Se bombea agua fría o algún otro líquido refrigerante a través de estos canales, hacia adentro y hacia afuera, mientras la herramienta realiza ciclos constantes de frío y calor.
¿Entonces, cuál es el problema?
Si la parte dentro de la cavidad es perfectamente cuadrada y plana con bonitos bordes rectos, entonces los canales de enfriamiento se pueden hacer para que coincidan con esas superficies a unos pocos milímetros de la cavidad. Esto permitiría que la pieza se expandiera y contrajera uniformemente, evitando así la posibilidad de deformación.
Desafortunadamente, los diseños complejos de piezas de plástico rara vez son tan geométricamente simples. Los agujeros perforados rectos no pueden seguir curvas, nervaduras, protuberancias y otras formas intrincadas, por lo que la herramienta no se puede enfriar adecuadamente y la deformación se convierte en un peligro real. La antigua solución era que la herramienta necesitaba un período de tiempo más largo entre disparos para alcanzar el equilibrio y, por supuesto, los retrasos más prolongados ralentizaban la producción y costaban dinero.
¿Existe alguna solución?
Ahora, el software CAD 3D y la impresión de metal 3D permiten crear herramientas en acero o aluminio con canales de enfriamiento conformados que no se limitan a trayectorias lineales de herramientas como ocurre con los orificios perforados convencionales. Mediante la fusión directa de metales por láser (DMLM), se colocan capas delgadas de material una a la vez y se funden juntas para formar un todo sólido, creando canales que pueden seguir los contornos de la pieza dentro de la cavidad. Esta técnica avanzada acelera enormemente el tiempo de enfriamiento de la herramienta y al mismo tiempo reduce el riesgo de deformación y mejora la consistencia y calidad de las piezas.
¿Qué hay de malo en las líneas de soldadura?
En la imagen de arriba puedes ver dos pequeñas marcas al lado del racor roscado. Estas son líneas de soldadura y se crean cuando se inyecta plástico fundido en la cavidad y se obliga a rodear el poste de metal en el molde que hace ese agujero. Cuando los dos bordes principales del plástico se unen en el otro lado de ese poste, intentan unirse en una sola unidad completa. Pero las diferencias térmicas en la temperatura del molde y del plástico hacen imposible una soldadura perfecta, creando así esta marca característica.
Una línea de soldadura puede indicar un área débil en la pieza que puede fallar bajo tensión. Otras veces, es necesario cubrir esta costura, ya sea con un acabado superficial texturizado, lijado o pintura. En todos estos casos, esto implica tiempo, esfuerzo y dinero adicionales. En lugar de ello, al utilizar los mismos canales de enfriamiento conformados para enfriar el molde, se puede bombear un líquido de alta temperatura (~150 °C) a la herramienta que la calienta, eliminando este estrés térmico y permitiendo que el plástico fluya suavemente y se suelde por completo. , sin dejar ninguna línea de soldadura. Esto evitaría la necesidad de realizar más posprocesamiento, como pintar, y reduciría en gran medida el coste de la pieza acabada.
Fabricar una herramienta de moldeo por inyección de plástico con un inserto calentado es más costoso y lleva más tiempo, pero ofrece grandes ventajas en el producto terminado. Si la cantidad de piezas deseadas es lo suficientemente grande, el coste de la herramienta puede verse más que compensado por el menor coste de producción de la pieza terminada.
Equilibrar las tensiones térmicas de las herramientas de moldeo por inyección de plástico es solo uno de los muchos factores que se deben considerar al construir una herramienta exitosa. Pero la impresión 3D ahora pone a disposición una técnica que resuelve un problema antiguo y permite la creación eficiente de diseños completamente nuevos con un rendimiento excepcional. En Star Rapid, contamos con un equipo internacional de expertos técnicos que pueden explicarle cómo este proceso puede beneficiar su próximo proyecto. Contáctenos hoy para aprender más.
Enlace:Métodos avanzados para fabricar mejores herramientas de molde
Etiquetas importantes: fundicion a la cera perdida, Mecanizado de metales, Fabricación de moldes